当社では自動車の精密プラスチック部品から家電部品、オフィスチェアなどの金型を幅広く製作致しています。(50t~850tクラス)
- 自動車部品の金型
- 自動車部品の金型
- オフィスチェアの金型
製品の多様化・高品質化でユーザーの信頼を得るために、工作機械設備の充実を推進するとともに、先々まで長いお付合いが出来るよう若い技術者の育成にも力を入れて取り組んでいます。
アフターメンテナンスも承っておりますので、金型の清掃、経年劣化でバリが出て来たなど、お気軽にご相談下さい。
金型破損などによる緊急時にも、スタッフ現地派遣や休日出勤等で瞬時に対応する様務めています。
製作の流れ
1. お見積り・事前打合せ
お客様から提供された仕様書・2Dデータや3Dデータをもとに見積書を提出します。
2. 設計・加工データ作成
CADで型の3Dモデル作成し、直彫り加工と放電加工用電極モデルを作成
モデルを使用し、マシニング加工用プログラムの作成
マシニング加工で直彫加工を施し、隅部のみ放電加工で製作する
加工工程が多い放電加工を減らすことにより、コストダウンを図っている
3. 前加工(荒加工)
金型部品の穴明け・荒取り・仕上加工をします
4. マシニング加工
金型・型部品の切削加工をします。
5. 放電加工(仕上加工)
深リブ、ネジ部、エッジ部などマシニングによる加工が比較的に困難な箇所を加工をします。
6. 磨き
金型製品部を砥石・セラミック砥石・ダイヤモンドペースト等を使用
ほとんどが手作業で行っており、さまざまな形状を磨くことが可能
実体顕微鏡を見ながら形状を確認し、面粗度をあげます。
7. 測定
入子の測定・確認
寸法修正のための測定
工程ごとに各オペレーターが加工終了時点で測定作業を行い、次の工程に渡します。
8. 組立
各工程から完成したパーツ等の検査・調整・組込み作業
モールドベースを十分に仕上げ、各工程から完成した部品を
調整・組込みを行う
金型製造での最終工程となり、手作業がメインとなるため
ヒューマンエラーが起きないようチェックリストに記入し、最終チェックを行う
常にT0での良品を目標としている
量産立上げまでのアフターフォローを行っている
9. トライ
新型・設計変更及び修正後の成形確認
(形状・不具合・成形性・金型の作動)
お客様(メーカー)へ納品する前に成形を行うことにより、
ファーストトライの不具合の減少と品質向上につなげる
状況によりお客様のもとに伺い、トライ立会い・調整等を行う
設備・マシンリスト
マシニング、放電、ワイヤー、研磨。金型成型に必要な全てのマシンが整っており、スピーディな加工を実現致します。
- 三菱 EA 12V ADVANCE
- 牧野フライス製作所 V33
- アサイ産業 DSP1300
※保有機一覧につきましては、下記画像をご覧下さい。
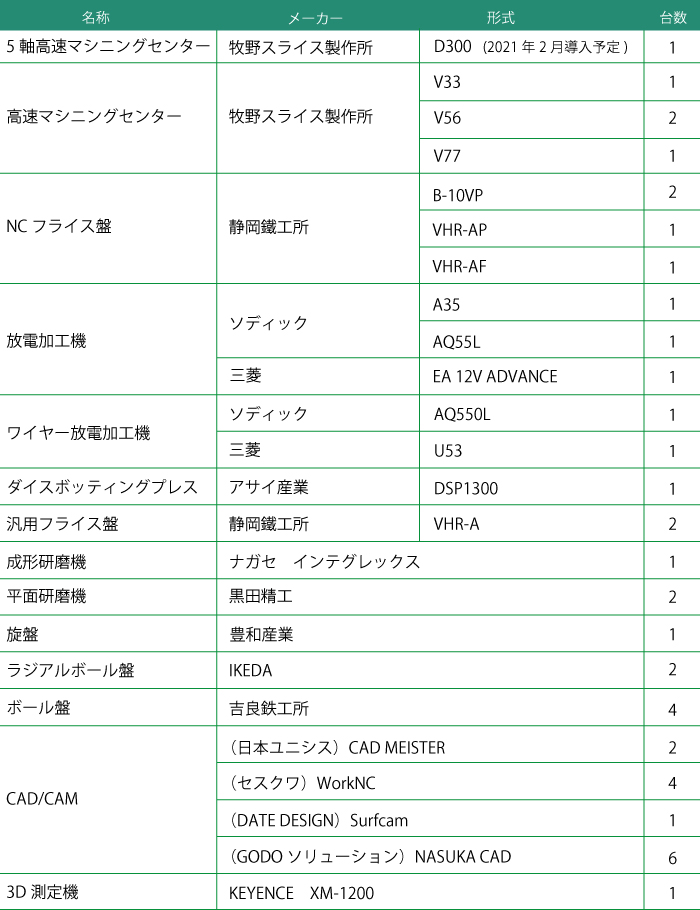